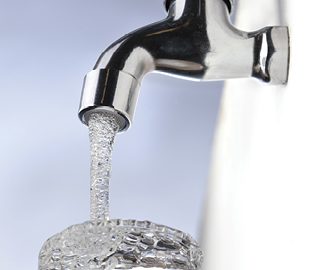
An excellent screenings solution for applications requiring removal of small particles, the Raptor® Rotating Drum Screen’s high removal efficiency meets the needs of Membrane Biological Reactor (MBR) designs. Using either a perforated plate or wedge wire basket with openings ranging from 0.02 to 0.25-inches (0.5 to 6 mm) this screen is ideal for either municipal or industrial applications. Captured screenings are compacted, dewatered and washed free of most organic materials to approximately 40 percent solids. Volume is reduced by 50 percent and weight by 67 percent, thereby reducing disposal costs.
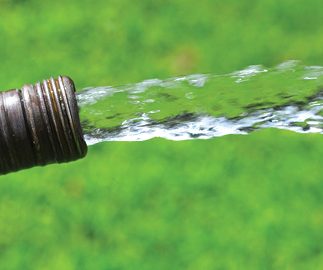
An economical treatment system to biologically process wastewater, the efficient Extended Aeration Treatment Plant provides superior performance in meeting your effluent discharge limits. The compact design is suitable for small communities, housing developments, trailer parks, schools, and industrial applications.
The E.A. Aerotor Plant is constructed in a concentric common wall design that incorporates the Closed Loop Reactor (CLR) Process in the outer loop for extended aeration and mixing, while the inner area has the peripheral-feed Spiraflo Clarifier for final settling. Alternatively, a second outer channel could be added for stand-by capacity, allowing efficient treatment for seasonal flow variations and promoting biological nutrient removal.
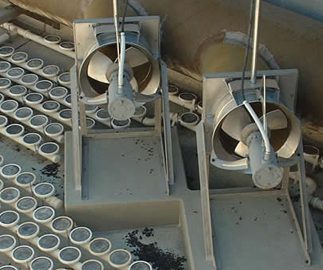
Submersible mixers and recirculation pumps are an excellent complement to the Sequencing Batch Reactor (SBR) and Closed Loop Reactor (CLR) Process that are designed for Biological Nutrient Removal (BNR) applications or energy conservation. The mixers and pumps have a stainless steel propeller that is shaped for optimum flow and a highly efficient planetary drive resulting in low energy consumption.
Low and medium speed submersible mixers are used to thoroughly mix the contents in the anaerobic tank, anoxic tank, or CLR aerobic reactor. This helps reduce power costs in low flow start-up conditions, where oxygen requirements are well below the mixing needs. In denitrification applications, the submersible mixer and aeration are cycled to provide anoxic and aerobic conditions within the SBR or CLR reactor for total nitrogen reduction.
Recirculation pumps are provided in denitrifcation applications to recycle mixed liquor from the aerobic basin back to the anoxic stage. The recirculation pumps are designed for high efficient pumping of large quantity of liquid at low head, which makes it ideal for BNR processes.
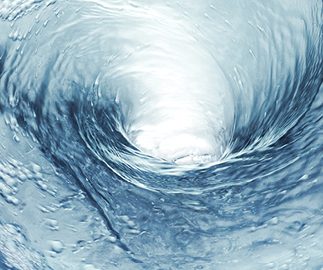
The Spiraflo is a peripheral feed waste clarifier designed for superior removal of suspended solids that could be used in a primary, secondary or tertiary clarification system. The wastewater enters the outer perimeter of the clarifier tank and is directed along the narrow raceway formed by the skirt and the outer wall. This flow pattern dissipates the wastewater’s hydraulic energy as it flows around the raceway, eventually spiraling down underneath the skirt and into the main settling area. The flow travels inward from the skirt towards the center of the tank, coinciding with the direction of the sludge, and the clarified water rises into the centrally located effluent weir trough. The combination of the spiraling flow pattern and the skirt eliminates all possibility of short-circuiting and provides better utilization of the total tank volume for more effective settling. Our wastewater clarifiers are designed to seamlessly remove solids and any impurities from wastewater.
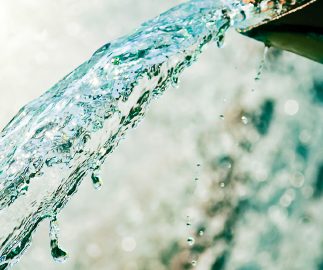
The Spiravac is a peripheral feed clarifier designed for superior solids removal through suction orifices to ensure rapid return of active sludge to the process. The wastewater enters the outer perimeter of the clarifier tank and is directed along the narrow raceway formed by the skirt and the outer wall. This flow pattern dissipates the wastewater’s hydraulic energy as it flows around the raceway, eventually spiraling down underneath the skirt and into the main settling area. The flow travels inward from the skirt towards the center of the tank, coinciding with the direction of the sludge, and the clarified water rises into the centrally located effluent weir trough. The combination of the spiraling flow pattern and the skirt eliminates all possibility of short-circuiting and provides better utilization of the total tank volume for more effective settling.
The Spiravac Clarifier is available in two designs; the Controlled Removal (Type CR) which utilizes individual sludge removal pipes and adjustable riser pipes in a revolving sludge well, or the Direct Removal (Type DR) which uses a common header pipe with orifices that removes sludge to a rotating manifold at the center of the tank for withdrawal.
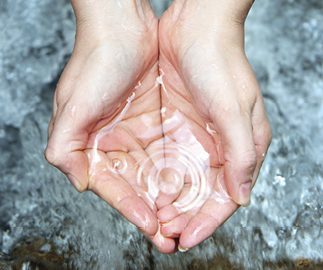
The peripheral-feed design significantly captures floating material in the clarifier’s outer skirt. This process may require full surface skimming to remove material in the main settling area. There are two types of full surface skimmers available:
The Motorized Full-Surface Skimmer extends the full width of the clarifier surface, from the effluent trough scum baffle to the outer race skirt. A drive assembly rotates the skimmer arm to clean the clarifier surface, and a hinged blade suspended from the skimmer arm pushes floating material to a rotating scum trough for removal.
The Full-Surface Ducking Skimmer is an economical alternative to the Motorized Full-Surface Skimmer. The full surface skimmer, which is supported by the clarifier’s scraper arms, moves the floating material to the scum trough for removal. The skimmer supports are hinged to allow the skimmer to duck underneath the scum trough during the removal process.
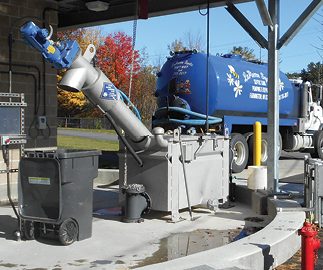
Remove debris and inorganic solids from septage tanks, grease traps, sludge, leachate and industrial waste with the fully automated Raptor® Septage Acceptance Plant (SAP). The heart of the SAP is the Raptor® Fine Screen, which compacts and dewaters the captured screenings to a solids content of 40 percent. The screen’s rotating rake teeth fully penetrates the cylindrical screen bars, which prevents plugging and blinding from grease and small debris. This allows for faster unloading times to generate more revenue for your facility.
The Raptor® Acceptance Control System (RACS) is a security access station that can be integrated with the SAP to allow authorized haulers to unload their waste at your facility. Adding the data management and accounting system with the RACS station provides administration capabilities to track and invoice customers.
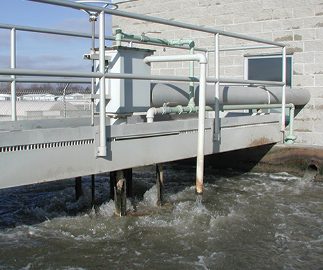
The Aeroductor grit chamber effectively removes inorganic grit from the influent flow in a controlled, aerated environment. Air is injected into the grit chamber, circulating the contents and causing lighter organics to remain in suspension while heavier grit is scoured, washed and collected at the bottom of the tank. Settled grit is periodically removed by an airlift pump. The air-grit slurry mixture is lifted to the head box where the air is vented and the liquid/grit mixture is directed to the Grit Classifier for separation and dewatering.
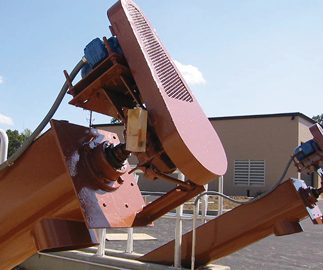
Ideal for smaller treatment facilities, the In-Line Grit Collector is an aerated grit chamber. It is an all in one unit consisting of a settling chamber with an air diffuser, grit screw, and an effluent trough. Air maintains circulation in the grit chamber for all flow conditions keeping lighter organic material from settling. The heavier grit particles, which settle to the chamber floor, are removed by an inclined grit screw for disposal.
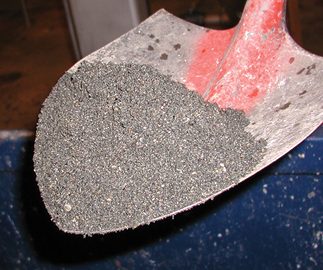
The Raptor® Grit Washer effectively washes and stirs the grit ensuring only cleaner, dense grit remains. Combining a circular and conical design with natural vortex and gravity forces, the washer provides the highest washing efficiency over a wide range of flow rates.
Influent flow enters the all stainless steel unit tangentially, creating centrifugal forces that allow water and lightweight organics to discharge over an upper weir plate. Grit and heavier materials settle to the lower conical shaped grit zone where they are gently agitated by mixer arms and washed. Organics released during agitation and washing are removed periodically via a blow down valve maximizing grit removal operations.