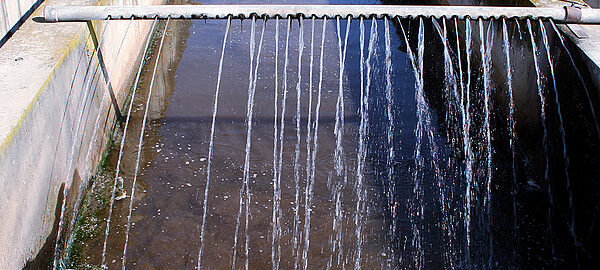
Water is essential to daily life in so many ways, and we couldn’t live without it. Water treatment facilities are responsible for taking wastewater and treating it to remove contaminants before it makes its way to our soil and natural water resources. To accomplish this, wastewater treatment facilities can use either biological or chemical water treatment methods.
Both methods are effective, but they work differently and are best used in different scenarios, against specific types of contaminants. Let’s take a closer look at both biological and chemical treatment methods, and how they’re different.
What Is Biological Water Treatment?
Biological water treatment is a process where microorganisms, such as bacteria, are used to eliminate organic matter in the water. Microorganisms essentially consume and break down organic matter. The organisms used in biological water treatment thrive and are robust in environments such as wastewater that contains organic pollutants. Through microorganism consumption, harmful pollutants are converted into less harmful byproducts.
There are two different processes used in biological water treatment. The first is aerobic wastewater treatment. With this method, microorganisms that require oxygen are used. Wastewater is transferred to an oxygen-rich environment where microorganisms can get hard to work breaking down contaminants. Wastewater treatment facilities that treat sewage will often use an aerobic process when using biological water treatment.
The other process is anaerobic treatment, which is the exact opposite of aerobic treatment. In this case, microorganisms that can thrive in environments void of oxygen are used. This process is fermentation, much like how fermented foods, such as pickles or sauerkraut are created in an oxygen-free environment. Anaerobic treatment is effective for certain types of waste, such as the sludge left after wastewater treatment.
Understanding Chemical Water Treatment
Chemical water treatment relies on chemical reactions to remove pollutants from wastewater. Chemicals are added to wastewater to neutralize the pollutants. Once the chemicals are added, a chemical reaction occurs, resulting in the contaminants separating from the water so that they can be easily removed. Other times, chemicals are added to kill potentially harmful pathogens. Water that has been chlorinated is a common example of this.
A benefit of chemical water treatment is that it is very fast and effective. In situations where wastewater must be treated quickly, chemical treatment is typically the preferred route.
How Are They Different
Both biological and chemical treatments are effective for cleaning wastewater. Wastewater treatment facilities need to consider the differences between the methods, rather than the similarities when choosing which process to use.
The most obvious difference is the nature of the treatment. Biological treatment removes contaminants through a natural process that breaks down organic waste. Chemical treatment relies on the use of chemicals to either kill, neutralize, or remove pollutants from the wastewater.
From an efficiency standpoint, chemical treatment is much faster. However, biological treatments may be preferred when there isn’t a sense of urgency or reason for the wastewater to be treated quickly.
Each method has applications that it is best suited for. With biological treatment, it’s most effective at breaking down various types of organic matter. This would include organic materials such as plants, food, and human waste. For this reason, biological treatment is generally preferred for sewage. On the other hand, chemicals are effective at breaking down pollutants that microorganisms aren’t effective against. This includes pathogens and pollutants such as heavy metals.
There’s also an environmental impact for each type of wastewater treatment. Biological treatments are considered to be more environmentally friendly. When microorganisms are introduced to wastewater treatment environments, the process is a natural one. In contrast, chemical treatment can lead to toxic byproducts, which present their own issues with removal and management. Chemical treatment can be exponentially more effective in certain cases, but it does require more careful thought and handling.
Pros & Cons of Biological Vs Chemical Water Treatment Methods
Biological Treatment Pros
Natural and Eco-Friendly
Cost-Effective
Energy Efficient
Sustainable
Helpful Byproducts
Biological Treatment Cons
Only Effective Against Organic Matter
Slower Process Than Chemical Treatment
Requires More Monitoring and Can Be Difficult to Manage
Chemical Treatment Pros
Extremely Efficient
Fast-Acting for Times When Waste Water Needs to Be Treated Quickly
Effective Against Pathogens and Toxic Contaminants Like Heavy Metals
Requires Less Monitoring, Easier to Manage
Chemical Treatment Cons
Potential for Toxic Byproducts
Less Environmentally Friendly
More Expensive Option
Less Sustainable
Exposure to Dangerous Chemicals
Best Uses for Biological and Chemical Treatment Methods
Using the right wastewater treatment method means a more efficient process and cleaner output. Treatment facilities need to consider the types of pollutants they need to clear from the water, along with other factors in deciding which process to use.
Chemical wastewater treatment serves an important role. It’s the primary means of disinfecting potable water. With new initiatives supporting the reuse and recycling of wastewater, effective and safe chemical treatments are important.
For example, chlorination is effective in killing harmful pathogens. The level of chlorine used for disinfecting drinking water isn’t the same as what’s used in swimming pools, which many people are familiar with. The tap water that comes from your faucet has likely been treated with a low level of chlorine to kill organisms you don’t want anywhere near your food, beverages, or skin.
Treatment facilities that handle medical wastewater, such as from hospitals, face unique treatment challenges. A combination of pharmaceutical residue, chemicals, and pathogens, requires an approach to effectively treat the water so that it’s safe for disposal. In this scenario, chemical treatment is the safest option.
Chemical wastewater treatment is also used when heavy metals, such as lead, mercury, or arsenic are involved. These metals cannot be degraded using biological methods, so the industry turns to chemical treatment to ensure compliance with wastewater regulations.
While chemical treatment is highly effective in these cases, it’s not a viable option for all treatment facilities. Municipal wastewater treatment plants often turn to biological treatment which is ideal for organic matter found in domestic wastewater and sewage. By using microorganisms, municipal wastewater becomes safe to release into natural water sources.
The same is true for agricultural wastewater treatment, which typically contains significant amounts of organic waste. This includes everything from organic plant residue to animal waste. A major benefit of biological treatment in this case is the generation of biogas.
Biogas is a renewable energy source generated from the breakdown of organic matter, such as that found in agricultural wastewater. Biogas has many potential uses including being transformed into fuel for vehicles.
Industrial wastewater can be high in contaminants best suited for chemical treatment, but this isn’t always the case. Industrial wastewater from industries like food and beverage produces a high level of organic matter that can be mitigated through biological treatment.
The dairy industry is a great example of this, as biological treatment can be used to degrade organic waste produced as a result of bovine milk processing. Breweries, both macro and micro also produce wastewater filled with organic pollutants, necessitating the use of biological treatment agents.
Biological and Chemical Treatment Are Both Important
Biological and chemical wastewater treatment processes each have pros and cons, but each is important for effective and safe treatment. In the United States, each individual person produces as much as one hundred gallons of wastewater each day. Utilizing both wastewater treatment methods and continually looking toward new, innovative methods, allows the industry to manage wastewater in the most effective way.
At Lakeside, we’re committed to providing our customers with the safest and most effective wastewater treatment equipment to meet their needs. If you have questions about wastewater treatment equipment or the processes of biological and chemical treatment, we’re here to provide answers. Contact Lakeside Equipment today