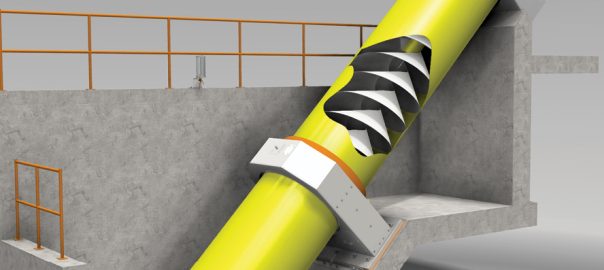
Open and enclosed screw pumps are used in a variety of settings. They’re often found in wastewater treatment plants where they move sludge and fluids that travel in through sewer lines or from hauled septage. Screw pumps are also helpful in commercial applications, though people don’t always stop to think of the benefits of screw pumps in a commercial setting. Here are five commercial applications for screw pumps.
Beverage Industry
The beverage industry is the perfect example of a commercial business that benefits from screw pumps. Breweries, wineries, kombucha, canned/bottled coffee, and other beverage companies can move liquids around without damaging other components in the recipe. As screw pumps require little maintenance and have the option of a Sealed Precision Type “E” bearing assembly that has a sealed bearing that doesn’t require a grease pump or grease lines that could leak over time and contaminate the liquids the screw pump is moving.
For example, beer is made by heating crushed grains (malts) with water. The liquid sits to extract the malt and must be separated. Using a screw pump, the liquids and grains are separated. Grains can go to farms as livestock feed. The remaining liquid is boiled and flavoring hops are added in stages. That mixture cools and yeast must be carefully added. As you add the liquid yeast mixture, a screw pump can control the speed so that it’s evenly mixed. Kombucha and wine are also beverages that are fermented and may benefit from a screw pump.
In winemaking, a screw pump can move fluid. It also moves the denser items like the dregs that include grape skins and seeds. The screw pushes the dregs to a container and the remaining liquid is piped to fermentation vats.
Screw pumps can also be used in a large kombucha plant. The screw pump can help during the step where tea leaves are removed from the tea right before the tea mixed with the culture that grows the SCOBY for fermentation. After the kombucha is moved to a cooling vessel and flowers, herbs, and other flavoring ingredients are added, you could also use a screw pump as it’s moved to kegs for carbonation.
Chemical Plants and Oil Refineries
While centrifugal pumps have been considered the normal option for a chemical plant, screw pumps are ideal. One of the leading reasons is to keep costs down. Screw pumps are designed to handle liquids of different viscosities. A centrifugal pump has to lower the flow rate when pressure increases. That requires constant adjustment to prevent problems. Screw pumps don’t need to make these adjustments, so you’ll save time and money. If you look at some of the flow rates of Lakeside Equipment’s different screw pumps, you’ll see the variation.
- An open screw pump can handle 90 gallons up to 55,000 gallons per minute.
- A Type C enclosed screw pump can handle 540 gallons to 35,000 gallons per minute.
- A Type S enclosed screw pump can handle 90 gallons to 10,000 gallons per minute.
Screw pumps are proving to be the best choice in the oil and gas industry. With more viscous crude oil coming in from countries like Canada, Latin America, and South America, it can take more work to move the oil from reservoirs to oil pipelines. With other styles of pumps, pressure changes required the pumps to be adjusted by the operator to prevent problems. Screw pumps can do this efficiently as they can handle different viscosities and changing pressures with ease. To maximize production, it’s important to work with an expert to help find the best type of screw pump for your refinery.
Food Processing
How could a screw pump be useful in food processing? When food processing requires delicate speeds to prevent over-mixing or adding items too quickly, a screw pump is ideal. A canning company needs to get diced tomatoes into a canning line without pumping the tomatoes so quickly that the tomato pieces get broken down. That’s one area where a screw pump is helpful. It moves the tomato mixture at the right speed to prevent damage to the tomatoes. Steady flow rates keep lines running effectively without much need for maintenance, which boosts productivity.
A cheese manufacturing plant is another example. Milk is trucked to the plant and pumped into the storage tanks before pasteurization. To make the cheese, the curds and whey have to separate. After this happens, whey is pumped away and curds move to the machinery that shapes them into a block or round of cheese. Throughout this process, screw pumps help move liquids or curds to the next step in cheesemaking.
Screw pumps can also help move the whey that’s left behind. Liquid whey is used for animal feed. Whey can be dried into a powder and used as a protein supplement and in baby food. It can be used in bakeries or added to foods like soups and salad dressings. Whey protein powder is a hot commodity, but you need an effective way to pump it to the tanks where it’s stored until it’s needed.
Paper Mills
The pulp and paper industry requires several screw pumps throughout the process. At the very beginning of the process, wood is stripped of its bark and chopped into tiny fragments that are soaked in a mixture of water and chemicals to help digest it. The resulting pulp has to have most of the liquid removed before it moves to bleaching and washing. After washing, a new round of water removal takes place. The pulp goes through a refining process before heading to the paper making presses and drying area. Each new step that requires the separation of liquids benefits from a screw pump.
Eventually, the resulting liquid (liquor) has to be purified. The water left over after paper is made often go into ponds or tanks that use aeration to add oxygen and help with the water treatment process before it returns to bodies of water. The remaining sludge is often sent to incinerators.
Theme Parks
Theme parks across the country rely on screw pumps. Any theme park with a water ride needs a way to get water to the top of a ride or slide where it can plummet down the slide or track to the pool below. A screw pump is effective at moving large amounts of water continually. If you think about water parks where there are log rides in a flume, a screw pump is good at bringing water from the pool back up to the top of the ride over and over. The same is true of water slides and water rides where riders either use an inflatable tube or ride through the slide chute independently. If the water stops flowing, the ride goes wrong. It’s important to have low-maintenance screw pumps moving water non-stop from the bottom to the top.
Lakeside Equipment offers both enclosed and open screw pumps. Our first designs go back to the 1960s and have seen many improvements over the decades. With more than 50 years of expertise, we specialize in clog-free designs. You’ll work with an experienced team to match both your budget and specifications. Trust in us to design a screw pump for your industrial setting.