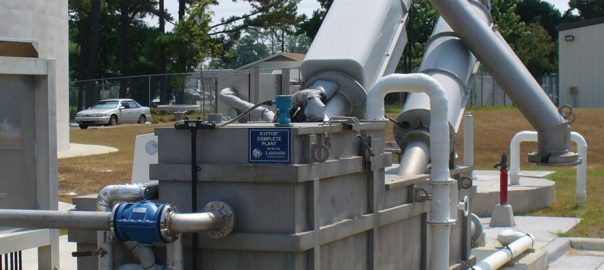
Many companies in the food and beverage industry create massive amounts of wastewater each day. Take beer for example. A pint of beer is around 95% water, but far more water is used up making that pint of beer. It’s estimated that you need as much as seven gallons of water to make one gallon of beer. Of that, about 70% of that water is discharged as wastewater to city sewers.
Now, think about it this way. The entire U.S. beer industry sold just over 203 million barrels of beer during 2019 One barrel is about 31 gallons, so about 6.29 trillion gallons of beer were sold in 2019. That means more than 44 trillion gallons of water were used to make all of that beer and an estimated 30.8 trillion gallons became wastewater.
That’s just the beer industry. If you think about all of the other food and beverage industries that produce wastewater, it’s easy to see how problems arise. If you have a wastewater district that accepts wastewater from the area’s breweries, meat processing plants, dairy plants, wineries, etc. that’s a lot of liquid. Too much poses the risk of overwhelming a plant. If the wastewater is released before it’s treated, it can harm the area’s wildlife and increase pollutants in area water sources. This is why it’s so important for the food and beverage industry to carefully consider wastewater solutions.
What’s in Your Wastewater?
You need to consider what’s in the effluent you produce. Wastewater treatment plants must meet local, state, and/or federal guidelines on the contaminants in water that’s released. Bacteria like coliform must meet the maximum levels. Restrictions are also in place for things like biological oxygen demand, chemical oxygen demand, phosphorus, nitrogen, and total suspended solids.
Breweries often produce high levels of nitrogen and phosphorus. That’s the first part of the problem. Grains and hops must be filtered to prevent them from clogging lines. Plus, the gritty grains can damage equipment. There’s also the sludge from the yeast. If you’re a contributor to the higher levels of suspended solids, bacteria, and nutrients, you may pay sizable fees to be connected to that wastewater district.
A plant that processes poultry, pork, or beef may contribute to higher coliform counts due to the animals’ intestinal tracts and feces that are removed and rinsed from the floors. Ammonia counts can be higher with larger animals that urinate on the floors. Fat from the animal and its blood also poses a problem.
Dairy plants that make cheese or yogurt have bacteria that are flushed away at the end of the production cycle. Like a meat processing plant, there are also fats and greases to consider.
How Can Companies Better Manage Their Wastewater?
If you look at the amount of water used by many companies in the food and beverage industry, it’s substantial. The amount of wastewater produced is also immense. It often becomes cost-effective for companies to recycle their water for reuse or start the cleaning process before the effluent goes to a local wastewater treatment plant. These companies have implemented wastewater solutions within their businesses.
Alchemist Brewery in Vermont
Take Alchemist Brewery in Vermont for instance. The popularity of Heady Topper and Focal Banger had people coming from around the world to try the beer. When the demand became too much at their second facility, they decided to open a visitor’s center in Stowe and open a cannery in Waterbury. The brewery has a lot of organic matter from the yeast, hops, grains, and malt sugars. They started sending them to Vermont Technical College’s anaerobic digesters to create energy and fertilizer for area farms.
At the same time, the visitor center had room for the brewery to put in its own water treatment system. The wastewater goes into a settling tank before going to the pumping tank. Solids go to an aerobic digester where as much as 6,500 gallons are treated each week. The water that’s sent back to the water district is already cleaned, which lessens the impact on the wastewater treatment plant.
Two Cheesemakers Install Their Own Wastewater Treatment Plants
Cheesemakers process a lot of cream and milk with cultures that turn it into curds and whey. Those curds become some of the cheeses people buy at specialty shops and grocery stores. Not only is water consumption high, but the whey and bacteria become a lot for a water treatment plant to process. Rothenbühler Cheese aimed to solve this by adding an on-site water treatment plant.
A few years ago, Rothenbühler Cheese hired a wastewater treatment expert to design and install an anaerobic wastewater treatment system containing pumps that send the wastewater to a digester tank. It continues to a membrane bioreactor. The biogas that’s produced during water treatment is captured and used in the plant’s dual-fuel boiler.
Montchevre is another cheesemaker that installed an anaerobic digestion system after weighing the pros and cons of anaerobic digestion and sequencing batch reactors (SBR). This system cleans the wastewater and produces electricity from the resulting biogas at the same time. While you might think the cost of installing such a system is expensive, they were able to use special funding programs from the government to afford the upgrades.
Sometimes Wastewater Districts Must Expand
Some wastewater districts expand their treatment plants instead. In North Carolina, production at the Tyson chicken processing plant steadily increased, but that also put the wastewater district at max capacity. Heavy rains were putting the plant at risk of releasing untreated effluent, which is not ideal. While the district has no restriction on the amount of wastewater that can be released into the area river, there are limits on the biological oxygen demand.
To resolve this problem, the town officials decided it’s time to upgrade the wastewater treatment plant to make sure that the equipment does an exceptional job of treating the water. With a plant expansion, the district cleans the water, releases it to the river, and doesn’t change the biological oxygen demand. Experts in wastewater treatment will help design the upgraded system.
If your town needs to look at increasing capacity, it’s important. Recover the cost by working with area food and beverage manufacturers to upgrade and enlarge your wastewater treatment plant.
What if You’re Short on Space?
A Package Extended Aeration Treatment Plant is a good solution for those in the food and beverage industry. It has a compact design, which is ideal for a company that doesn’t have a lot of space available.
What does this all-in-one water treatment system include? It’s designed to screen, aerate, clarify, disinfect, and contain sludge in one tank. This makes it very easy to install. You get a Closed Loop Reactor Process where the mixing and extended aeration take place in an outer loop before it goes to the inner Spiraflo Clarifier for the final settling process.
Is your water district looking for ways to be more cost-effective and efficient? Do you own a food or beverage company? If you think an on-site treatment plant could help your impact on your area wastewater treatment plant, see what it would take to build your own small plant. You may find you save money by reducing or stopping the fees you pay to be part of that district.
Lakeside Equipment’s specialists help design systems of all sizes. Let us know what your goals are and what budget you have. We’ll help you establish a wastewater treatment system that matches your needs.