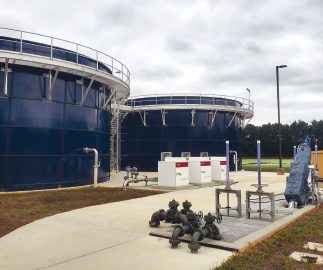
Running a wastewater treatment plant requires a lot of thought when it comes to safe operations, fiscal responsibility, and keeping an eye on future needs. A wastewater treatment plant manager has to know how to maximize any request for proposal (RFP). Any company can ask for bids for upgrades and repairs, but an RFP often takes a lot of negotiation and tough choices to lead to exceptional results.
How do you maximize your RFP for wastewater treatment? The most important decision you’ll make cannot be rushed. You want to give possible contractors a clear picture. From there, you’ll need to take your time selecting the best team for the work. These steps can help you arrange the best contractor for your needs.
Lay Out Your Goals
Make sure you clearly lay out your reason for the project, the current set-up, and what the goals are. Give a description of your municipality including how many miles you serve, the population, and any budgetary information you can share. How is the wastewater treatment plant funded? Is it through property taxes, fees, grants, etc.?
Go over the budget for any improvements or repairs. The companies that you’ll work with do need to know if your financial goals are manageable. For that budget, what do you expect?
While you’re going through your goals, bring up the purpose for the RFP. Are you looking to be more efficient or increase the number of households you support? You want to choose a wastewater treatment contractor who meets local, state, and federal laws and regulations. Make sure you’re clear regarding how long you plan to work with this contractor. Will you be working with the contractor just for this project or are you also looking for someone to help with the repairs and maintenance over the decades?
As you discuss repairs and maintenance, you’ll want to cover other aspects of wastewater management like the management of construction workers and projects. You may want to work with a contractor who will arrange where the biosolids go when they’re removed during the wastewater treatment process. Will they be helping secure the chemicals and required testing?
Create a Complex Picture of Your Treatment Plant
When you’re writing out your RFP, present a full picture of your current plant’s design. You want to share the location, your acreage, the current layout, and the equipment you own. Talk about the plant’s capacity and average daily flow. Your plant should have a permit from the EPA, what is your NPDES permit number?
Once you go over what you currently have, discuss what the improvements need to include. If you’re often reaching your plant’s maximum daily flow, you’ll want to increase that. Where do you need the new plant capacity to be? Are you adding grit removal, improving your screens, or seeking energy-efficient changes? Do you want equipment that requires less routine maintenance?
When the water is treated, where does it go? Does it go into a local body of water or into water storage or reservoirs where it goes back to homes and businesses in that municipality? What types of pump stations are needed to get the water from these storage tanks or reservoirs back to homes and businesses? That’s another consideration that your RFP must mention. Give a list of locations and their flow rates.
Through each step of wastewater, including pump stations and reservoirs, is the city responsible for maintenance, or are you looking for a contractor to arrange the maintenance in these areas? Do you want the contractor to help find the right maintenance crew?
Be Clear About Contact Information
Provide updated contact information for possible contractors who have additional questions. Provide both phone and email and check messages at both. Some people may have more time to respond by email than phone or vice versa. If you’re amenable to both contact methods, you’ll get more responses. Give a deadline for questions so that you have time to answer them and schedule interviews and plant tours.
Take time to answer everyone. Even if the answer is “we’re going a different way,” it’s common courtesy to give a response. If you ever are in a position where you’ll need to work with a different contractor in the future, you haven’t upset anyone by ignoring their questions or proposal.
Don’t Forget the Equal Opportunity Requirements
It is your legal responsibility to make it clear that you will not be engaging in any discriminatory practices. When you select a contractor, you’re not basing your decision on gender identity, race, nationality, disability, religion, etc. You welcome everyone to apply, including veterans and aged workers.
Arrange a Tour Date and Timelines for Decisions
For contractors to come up with the right quote, they need time to tour the facility. Provide tours on a few dates so that every interested contractor can find a date that works with his or her schedule. Make sure you’re there for the tour and address any questions that arise during the tour.
About a month after the tours take place, set that as the date you require all proposals to be submitted. If you’ll be interviewing, follow the proposal deadline with the interviews. You want to narrow down your list of contractors shortly after the interviews.
Once you have selected your first choice, start the negotiation process. That will be the final step to awarding the contract to the winning company. In all, you want to do this at least six months before you want your project to start. That way, the contractor has time to schedule the project and get the equipment and supplies ordered in time.
Give Clear Instructions for Proposal Submissions
Give a step-by-step guide to how proposals need to be submitted and where they need to be delivered or mailed. If you want multiple hard copies and/or a PDF proposal, be clear about it. Give a date and time for those proposals to reach your office. Include the name, address, fax number, and email. Finish this up with a statement that you are not responsible for mail delays or lost emails and faxes if you even agree to receive the proposals electronically.
You want contractors to detail their qualifications, experience, cost proposal, and project details. Training and qualifications need to be given to every person who will be working on your wastewater treatment project.
Have a plan in place for any protests from contractors who are not awarded the contract or who become upset that they submitted a proposal that you never received. Give them a deadline to submit complaints and go over how to submit them.
Have a Back-Up Plan
What happens if you don’t like any of the proposals? Have a plan in place for this situation. If no one meets your needs, you’ll need to start the process over. While this isn’t ideal, you have to put the public and City budgets and needs first. If all proposals are too high or will take too long to complete, you may need to go back to the drawing board and see if there are ways to scale down your goals.
Be Open and Honest
As the public is usually the group paying for the cost of upgrades beyond any applicable grants, you need to be open and honest. Proposals have to be part of the public records for taxpayers to look at. Be clear about the scope of the project and why the improvements or project is needed.
If you take time with your RFP and are clear about the scope of the project, you’ll end up with great proposals. You don’t want to partner with a wastewater treatment contractor that leaves you and, therefore, your taxpayers hanging.
Lakeside Equipment has close to 100 years of experience in water treatment. We have a solid team of engineers who work with you during every step of your installation or improvements. We help you come up with a wastewater treatment design that matches your city’s needs and budgets. Give us a call to discuss your project.